Just how to Determine What is Porosity in Welding and Improve Your Technique
Just how to Determine What is Porosity in Welding and Improve Your Technique
Blog Article
Porosity in Welding: Identifying Common Issues and Implementing Best Practices for Prevention
Porosity in welding is a pervasive concern that frequently goes undetected till it triggers substantial problems with the integrity of welds. In this discussion, we will explore the crucial factors adding to porosity formation, analyze its destructive effects on weld performance, and talk about the finest techniques that can be adopted to decrease porosity occurrence in welding procedures.
Usual Reasons of Porosity
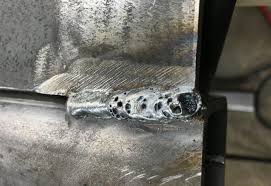
Utilizing dirty or damp filler materials can introduce pollutants into the weld, adding to porosity concerns. To minimize these typical reasons of porosity, complete cleaning of base metals, proper protecting gas choice, and adherence to optimal welding parameters are crucial techniques in attaining top notch, porosity-free welds.
Impact of Porosity on Weld Quality

The visibility of porosity in welding can substantially jeopardize the architectural honesty and mechanical residential or commercial properties of bonded joints. Porosity produces gaps within the weld steel, damaging its general toughness and load-bearing capability.
One of the main effects of porosity is a decline in the weld's ductility and sturdiness. Welds with high porosity degrees often tend to display reduced influence strength and minimized capacity to flaw plastically prior to fracturing. This can be especially worrying in applications where the bonded elements are subjected to vibrant or cyclic loading problems. Moreover, porosity can impede the weld's capability to successfully send forces, resulting in early weld failure and possible security threats in important frameworks.
Finest Practices for Porosity Prevention
To improve the architectural honesty and quality of welded joints, what details measures can be implemented to reduce the occurrence of porosity during the welding process? Porosity prevention in welding is important to guarantee the stability and stamina of the final weld. One reliable practice This Site is appropriate cleansing of the base metal, eliminating any pollutants such as corrosion, oil, paint, or dampness that could result in gas entrapment. Making certain that the welding tools remains in great condition, with tidy consumables and proper gas circulation rates, can also significantly lower porosity. In addition, keeping a secure arc and managing the welding criteria, such as voltage, present, and travel rate, helps develop a consistent weld pool that decreases the danger of gas entrapment. Using the correct welding strategy for the certain material being welded, such as adjusting the welding angle and gun placement, can better stop porosity. Normal assessment of welds and immediate remediation of any kind of problems determined throughout the welding process are crucial practices to avoid porosity and create premium useful content welds.
Relevance of Correct Welding Strategies
Implementing appropriate welding strategies is extremely important in making sure the structural integrity and quality of welded joints, building upon the foundation of effective porosity prevention actions. Welding methods directly impact the overall toughness and durability of the bonded structure. One crucial facet of appropriate welding strategies is preserving the proper warm input. Too much warm can result in boosted porosity as a result of the entrapment of gases in the weld pool. On the other hand, not enough warmth may result in incomplete fusion, creating prospective weak points in the joint. In addition, using the appropriate welding specifications, such as voltage, current, and take a trip speed, is vital for attaining sound welds with very little porosity.
Moreover, the option of welding procedure, whether it be MIG, TIG, or stick welding, need to line up with the details demands of the task to ensure optimum outcomes. Proper cleaning and preparation of the base metal, along with choosing the right filler product, are additionally vital parts of competent welding techniques. By sticking to these ideal practices, welders can reduce the danger of porosity development and generate top notch, structurally audio welds.

Examining and High Quality Control Procedures
Testing procedures are vital to spot and stop porosity in welding, this contact form making certain the strength and durability of the final product. Non-destructive testing techniques such as ultrasonic testing, radiographic testing, and aesthetic inspection are frequently utilized to determine potential flaws like porosity.
Post-weld inspections, on the various other hand, examine the last weld for any issues, consisting of porosity, and verify that it meets defined criteria. Executing a detailed quality control strategy that consists of comprehensive screening treatments and examinations is extremely important to decreasing porosity concerns and ensuring the general quality of welded joints.
Final Thought
Finally, porosity in welding can be a common issue that affects the quality of welds. By recognizing the common sources of porosity and applying ideal techniques for prevention, such as correct welding methods and screening steps, welders can make certain high top quality and reputable welds. It is necessary to focus on prevention methods to decrease the occurrence of porosity and keep the stability of welded frameworks.
Report this page